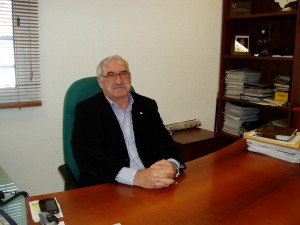
Ana Rodríguez. La empresa Antonio España e Hijos, S.L. está a las puertas de abrir sus instalaciones situadas en las antiguas naves industriales a la salida de Huelva por la carretera de Gibraleón. Desde su fundación en 1954, este negocio familiar ha ido creciendo y fomentando la cultura del reciclaje y la reutilización hasta alcanzar su estatus actual: ser la primera empresa en su sector a nivel provincial y de las primeras en Andalucía.
Tras mucho trabajo, ahora ponen en marcha una nueva planta, la de tratamiento de plástico agrícola, en la que podrán recuperar el film negro que se emplea en los campos y que, hasta ahora, era imposible de reutilizar. Pero ademas, antes de finales de 2013 también tendrán operativa una planta de reciclaje que enlazará con la anterior para, no sólo tratar el plástico sino también convertirlo en granza para fabricar objetos.
El presidente de Antonio España e Hijos S.L., José España, nos cuenta con todo detalle los planes de la empresa.
– La planta de tratamiento de plástico agrícola está a punto de abrir…
– Ya está prácticamente para ver la luz. Pensamos que en un mes y medio, dos meses como mucho, estaremos ya funcionado.
– Llevan dos años trabajando en este proyecto ¿no es así?
– El plástico lo empezamos a trabajar hace 25 años, pero hasta hace dos años no existía el reciclado para este tipo de material. Adquirimos una planta piloto en Alemania, nos la trajimos para nuestras instalaciones en junio de 2011 y prácticamente hemos tenido dos años de investigación, de experimentos, de desarrollo de nuevas tecnologías, de pruebas y de reformas. El resultado final ha sido positivo, hemos encontrado la fórmula para reutilizar el plástico film negro, que es muy difícil de reciclar. Si cargamos, por ejemplo, un camión de plástico tras retirarlo del campo, y éste pesa 10 toneladas, tres son de plástico y siete de tierra, pero además con el agravante de que nuestra tierra es muy abrasiva, altamente silícea y ello hace que, por un lado, destroce todas las cuchillas, los sistemas de trituración, de centrifugación, de lavado etc. y, por otro, que se incrusta, por las altas temperaturas del campo, la tierra, el agua, los fitosanitarios, etc. en el plástico y, como no se consiga disolver ,no se puede eliminar. Nosotros hemos conseguido esta disolución a base de experimentos, buscando aditivos a las aguas y sistemas adecuados para que la trituración del material no signifique un alto coste.
– ¿Ha sido difícil dar con la maquinaria adecuada?
– Hemos hecho miles de kilómetros a lo largo y ancho de todo el Mundo, visitando empresas de transformación de plástico, fabricantes de maquinaria y, al final, hemos conseguido hacer una planta que es única en el mundo. Tiene maquinaria adaptada adquirida en varios países. Tenemos maquinaria de la depuración de agua es italiana; de la trituración, alemana; de una segunda trituración, portuguesa; del secado del material, noruega; del embalado del material, danés; y maquinaria de segundo lavado de última generación también portuguesa. Maquinaria adaptada de sistemas de producción que no tenían nada que ver con el plástico pero que hemos conseguido que el fabricante nos la realizara conforme a nuestras exigencias y nuestros criterios para que cumpla la función que queremos.
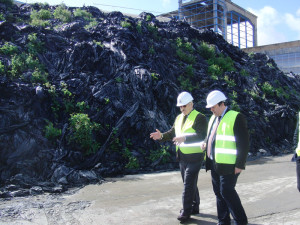
– ¿Y qué coste ha tenido todo ello?
– Las inversiones en maquinaria han sido del orden de tres millones de euros y las de adaptación de la planta y de obras, casi unos tres millones de euros. En total, la inversión ha sido de seis millones. Pensamos que podremos amortizar en diez años completamente la maquinaria y alcanzar beneficios.
– ¿A cuántas personas va a dar trabajo la planta?
– Va a haber tres turnos al día que abarcan a un total de 25-30 personas. Este personal, que tiene altos conocimientos en tratamiento del plástico, lo hemos ido formando en los dos años de investigación en la planta, aunque otros se han incorporado hace poco para que cuando la planta esté funcionando tengan claro su cometido. En trabajo indirecto, entre recogedores, clasificadores, transportistas, etc. más o menos la misma cantidad. Va a servir para que muchas empresas puedan seguir tirando, vamos a poder ofrecer trabajo a muchos recogedores locales y personas que se dedicaban al tratamiento y la recogida de residuos. También va a permitir que Hierros España siga adelante con los 150 trabajadores más que tiene en plantilla.
– ¿Cuál es el siguiente paso?
– Una vez que todos los sistemas que hemos puesto en vigor son adecuados, lo que nos queda es empezar a producir y mandar a nuestros clientes el material, aunque también tenemos la intención de poner una planta de reciclado. Queremos tenerla funcionando a finales de este año, tres o cuatro meses después de abrir y antes de que comience la campaña de recogida de plástico agrícola. Tiene una inversión menor y la instalación va a ser la misma.
El ciclo integral del plástico comienza con la clasificación, luego se tritura, se lava y se seca y pasa a una máquina que se llama extrusora, que funde el plástico y hace una especie de fideos que cuando pasan por una corriente de agua se enfrían, se condensan y se trocean y son los que hacen la granza. De ahí se meten en sacos y se envían al fabricante final. Sin embargo, antes de que tengamos la planta de reciclaje, nosotros nos quedamos en el secado y pasamos al embalado, vendiendo el producto resultante a nuestros clientes de China, Taiwán, India, Malasia, Brasil, Portugal y España para que ellos hagan la gransa. Cuando funcione la planta de reciclado, del secado se pasaría a ésta para completar el ciclo.
– ¿Cuántas toneladas de plástico van a fabricar al mes?
– De la planta de tratamiento van a salir todos los meses 2.500 toneladas. De la planta de reciclado es difícil saberlo, aunque podemos hacer una estimación de 500 ó 600 toneladas, intentaremos llegar a las 1.000, aunque será difícil; el resto, hasta alcanzar las 2.500, se enviaría fuera para el fabricante externo de granza.
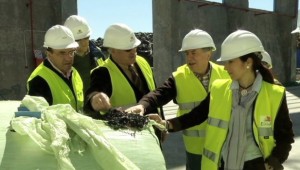
– ¿Cuántas toneladas de plástico van a poder reciclar en la planta?
– Ahora mismo tenemos en nuestras instalaciones 25.000 toneladas parar empezar a tratarlo. En el campo existe otro tanto que empezaremos a llevarnos poco a poco a nuestras instalaciones y que estará fuera del terreno en aproximadamente un año. Luego está la campaña de todos los años, que genera entre 15.000 y 16.000 toneladas de plástico negro y blanco anuales que antes se quemaban o enterraban y que ahora se va a recuperar con el consiguiente beneficio medioambiental. Además, acabamos de firmar un nuevo convenio para retirar los residuos de plástico de los campos por un periodo de cinco años en exclusividad.
– Tenían también un proyecto sobre una planta de combustible de residuos (CDR), ¿no es así?
– Correcto. En España ya las hay. Estamos trabajando en ello, parte de la planta piloto que se va a quedar paralizada una vez que lleguemos a la planta nueva, se va a utilizar en combustible derivados de residuos. Los residuos inertes que se recogen en la calle o en la industria se trituran y, en una proporción adecuada, forman el combustible que podrían utilizar las cementeras, las térmicas o cualquier tipo de industria que emplee calor en su proceso para obtener energía.
El problema es que no es obligatorio por Ley y las empresas tendrían que hacer una transformación importante de sus instalaciones y, ahora mismo, nadie se encuentra en condiciones de hacer esa inversión. Cuando lo hagan, que lo harán algún día, el CDR podrá ser en cualquier instalación un 20 o un 30 por ciento del combustible fósil, con lo cual estamos ganando en medio ambiente y en perpetuar la vida de los recursos fósiles. Por poner un ejemplo, sólo en Huelva se genera y tira al vertedero 2.000 toneladas mensuales, las cuales tienen el mismo poder calorífico que el petróleo o el gasoil y se podrían, por tanto, ahorrar esas 2.000 toneladas de combustibles fósiles, con las emisiones a la atmósfera que eso conlleva.
– Independientemente de la nueva planta, ¿a qué países exportan?
– Exportamos al mercado internacional. Enviamos metales férricos (cobre, latón, etc.) a China e India, por ejemplo, pero el 98 por ciento de nuestra producción va a los mercados nacionales, a las siderúrgicas sobre todo. En cuanto a los no férricos, a las fábricas de papel y cartón a nivel nacional y almacenistas que sí que exportan fuera.
España siempre ha sido un país importador de chatarra, necesaria para su industria. Ahora está todo parado pero en cuanto esto vuelva a sus orígenes volveremos a traer chatarra de fuera porque aquí va a hacer mucha falta cuando la industria nacional despegue de nuevo.
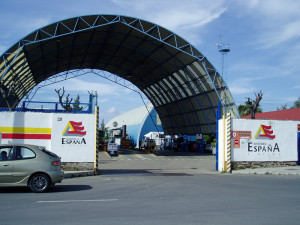
– En Hispanoamérica han abierto el mercado recientemente…
– Sí, estuvimos en Brasil hace menos de un año y abrimos mercado. Ahora estamos suministrándoles materiales. Tenemos intención de dirigirnos a Chile y Argentina y a todos los países de Europa que puedan estar interesados en este tipo de material.
– ¿Cómo terminaron el pasado año en términos económicos?
– Sin que hayamos experimentado pérdidas en la empresa, hemos estado muy justos. Afortunadamente, incluso con las inversiones realizadas, no hemos tenido problema en hacerles frente, pero la tónica de una empresa debe ser tener beneficios y esperemos que en los próximos años así sea.
– ¿Se está volviendo a los orígenes de lo que ha sido Antonio España?
– Nuestros orígenes fueron de chatarreros, luego fuimos recuperadores, ahora somos gestores y mañana seremos fabricantes de algo. Hay una evolución natural de la empresa conforme los acontecimientos se van sucediendo. Ahí radica la fuerza de esta empresa, que empezó siendo de un nivel familiar mínimo hasta que, poco a poco, hemos ido afianzándonos, viendo la evolución de los tiempos y no quedándonos atrás, hasta llegar a lo que hemos conseguido, a ser una de las primeras empresas de Andalucía en el sector. Nuestra tradición como empresa es ir siempre por delante en la innovación e insistir en nuestro lema de ‘Recuperar es mantener el medio ambiente’.
– Muchas gracias José